Burst Strength as Per MS 343-16
Why Burst Strength Testing is Essential for Quality Control – Insights from MS 343-16 Compliance
Introduction
- In the competitive world of manufacturing, the reliability of raw materials and finished products defines success. Whether you're in packaging, rubber goods, or textiles, ensuring your materials can withstand operational pressures is critical. One of the most effective ways to verify this is through Burst Strength Testing, especially when conducted according to the MS 343-16 standard.
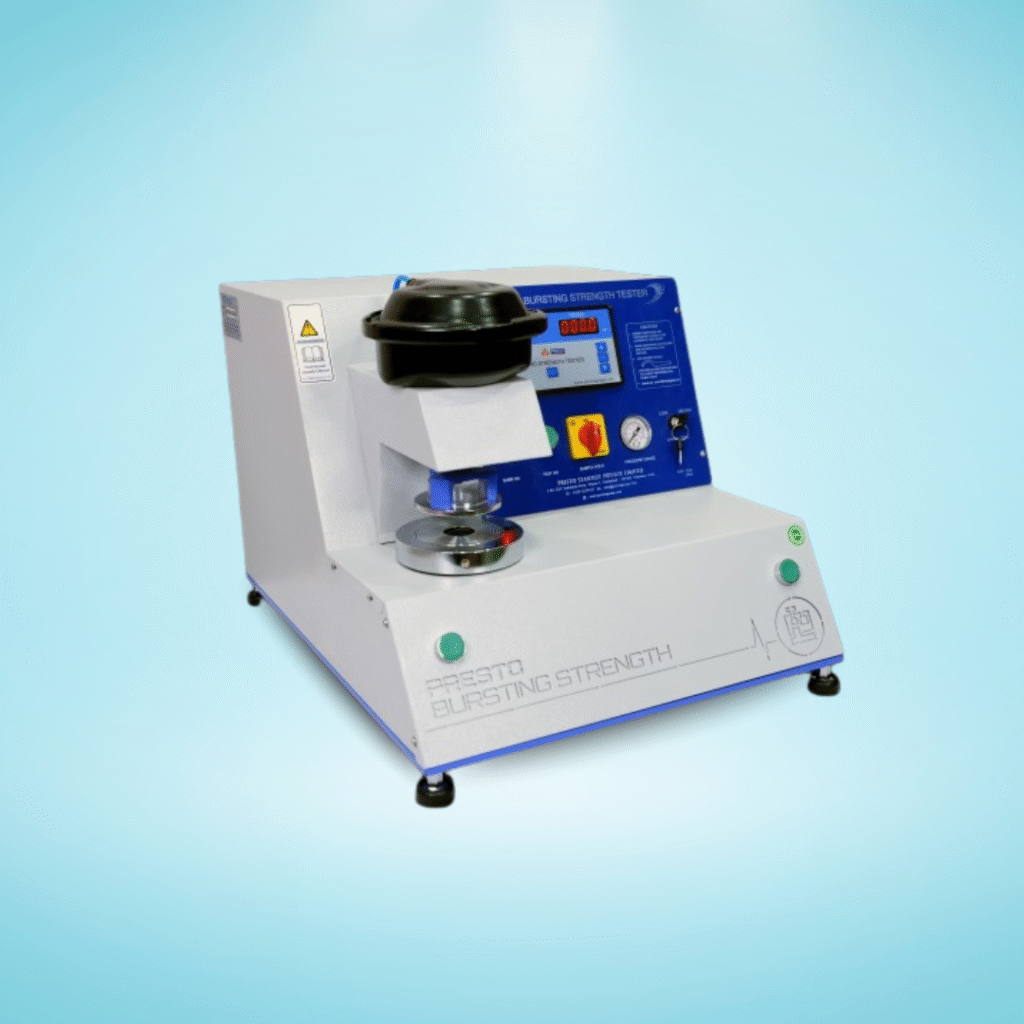
Understanding the Importance of Burst Strength
Burst strength refers to the pressure a material can endure before rupturing. This property is vital for materials exposed to internal or external pressure, such as:
Corrugated packaging for shipping
Rubber diaphragms and seals
Non-woven fabrics used in medical and industrial filters
Polymer sheets and liners
If a material fails under stress, it can result in costly downtime, product recalls, or even safety hazards. That’s where Burst Strength Testing steps in—offering predictive insight into material performance.
The MS 343-16 Advantage
At Kiyo R&D Center & Laboratory, we perform burst strength testing in strict adherence to MS 343-16, the Malaysian standard that outlines the correct methodology and conditions for the test. Compliance with this standard provides:
Repeatable and standardized results
Benchmark data for quality control
Assurance for both domestic and international markets
By following MS 343-16, manufacturers can gain confidence that their testing is both valid and recognized by regulatory bodies.
Use Cases Across Industries
Industries that benefit from burst strength testing include:
🏷️ Packaging: Ensuring boxes and cartons don’t collapse during stacking or transit
🚗 Automotive: Validating rubber seals and gaskets used in high-pressure systems
🧵 Textiles: Testing industrial fabrics that serve as filters or barriers
🧴 Plastics & Films: Evaluating strength of thin polymer sheets used in manufacturing
This test is especially useful for R&D teams developing new formulations or materials, as it helps predict product behavior in real-world applications.
Why Choose Kiyo for Burst Strength Testing?
Kiyo R&D Center is a trusted name in precision materials testing. Our fully-equipped laboratory, adherence to recognized standards, and fast, dependable reporting make us the preferred choice for quality-conscious manufacturers.
Our key strengths:
✅ Testing as per MS 343-16
✅ Trained lab technicians and calibrated instruments
✅ Supportive consultation for material improvement
✅ Results that support certification and compliance
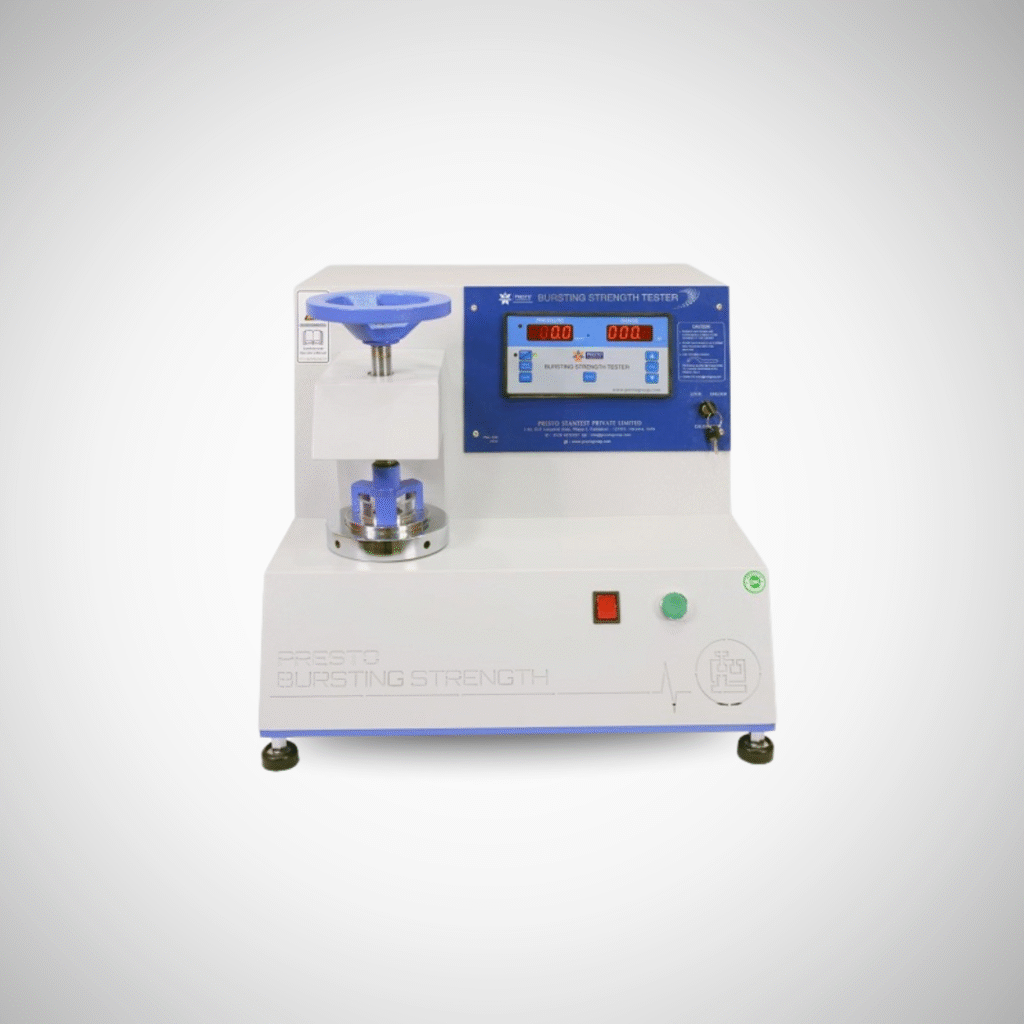
Conclusion: Build Quality with Confidence
- Burst Strength Testing is more than a checkbox—it’s an investment in product quality, safety, and customer trust. When done according to MS 343-16 at Kiyo R&D Center, you're not just testing strength; you're proving reliability. Ready to test your materials the right way? Let Kiyo help you build stronger, safer, and more compliant products.