Salt spray Resistance Test As Per Standard MS 655-08
Salt Spray Resistance Testing: A Crucial Assessment for Corrosion Durability as per MS 655-08
Introduction
- In today's competitive manufacturing environment, ensuring the longevity and durability of materials is paramount. One of the most critical tests to assess these qualities, especially for metals and protective coatings, is the Salt Spray Resistance Test. The MS 655-08 standard is a widely recognized guideline that provides a structured approach to conducting this test, particularly suited to the environmental conditions prevalent in regions like Malaysia. This blog explores the intricacies of Salt Spray Resistance Testing according to MS 655-08, highlighting its significance and the value it brings to various industries.
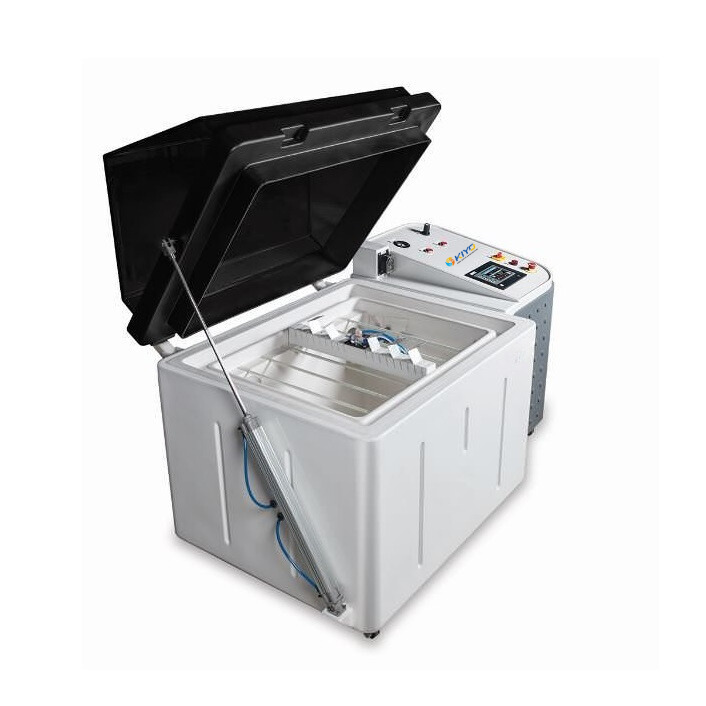
Understanding Salt Spray Resistance Testing
Salt Spray Resistance Testing, often referred to as salt fog testing, is a type of accelerated corrosion test. It is designed to evaluate the resistance of materials to corrosive environments, particularly those that involve exposure to saline or salt-laden air. The test involves placing a material sample in a chamber where it is subjected to a continuous saline mist, typically consisting of a sodium chloride solution. Over a specified period, this exposure simulates years of wear and tear in real-world conditions, allowing manufacturers to predict the material’s durability and resistance to corrosion.
Key Elements of MS 655-08 Standard
The MS 655-08 standard provides a detailed framework for conducting Salt Spray Resistance Tests. It ensures that the testing process is consistent, reproducible, and provides accurate results that can be relied upon across different applications. Key elements of this standard include:
Test Chamber Conditions: The MS 655-08 specifies precise conditions within the test chamber, such as temperature, humidity, and saline concentration. Maintaining these parameters is critical to replicating the corrosive environments that materials might encounter in the field.
Sample Preparation and Placement: Proper preparation of the test samples is crucial. The standard outlines guidelines on how materials should be prepared, including surface cleaning and placement within the chamber to ensure uniform exposure.
Test Duration and Evaluation: The duration of the exposure is another critical factor. Depending on the material type and its intended application, the standard provides guidance on the appropriate length of time the samples should remain in the chamber. Post-exposure, the samples are evaluated for signs of corrosion, such as rust, blistering, or pitting. The MS 655-08 standard sets the criteria for determining whether a material passes or fails based on the extent of observed corrosion.
Why Salt Spray Testing is Essential
Corrosion is one of the most pervasive challenges facing industries that rely on metal components and structures. It can lead to material failure, safety hazards, and significant economic losses. Salt Spray Resistance Testing is a proactive measure to combat these risks. Here’s why this test is indispensable:
Predictive Maintenance and Product Longevity: By simulating harsh environmental conditions, Salt Spray Testing provides valuable insights into how materials will behave over time. This enables manufacturers to make informed decisions about material selection, coating processes, and product design to enhance longevity.
Quality Assurance and Compliance: Adhering to standards like MS 655-08 ensures that products meet the required quality benchmarks. For industries such as automotive, construction, and marine, where corrosion can have severe implications, compliance with this standard is critical for maintaining product integrity and safety.
Cost Savings: Identifying potential corrosion issues during the testing phase allows manufacturers to address them early in the development process. This can prevent costly recalls, repairs, and warranty claims, ultimately saving the company money and preserving its reputation.
Industries Benefiting from Salt Spray Testing
Salt Spray Resistance Testing as per MS 655-08 is particularly relevant for industries that demand high durability in their products. These include:
Automotive Industry: For automotive manufacturers, ensuring that vehicles can withstand harsh weather conditions and road salt is crucial. Components like body panels, chassis, and fasteners are often tested for their corrosion resistance.
Construction Industry: Building materials, especially those used in coastal or industrial environments, must resist corrosion to maintain structural integrity. This testing ensures that materials such as steel rebar, metal cladding, and fixtures can endure exposure to the elements.
Marine Industry: The marine environment is one of the most corrosive due to high salinity and humidity. Salt Spray Testing is vital for evaluating the corrosion resistance of ship components, offshore structures, and marine equipment.
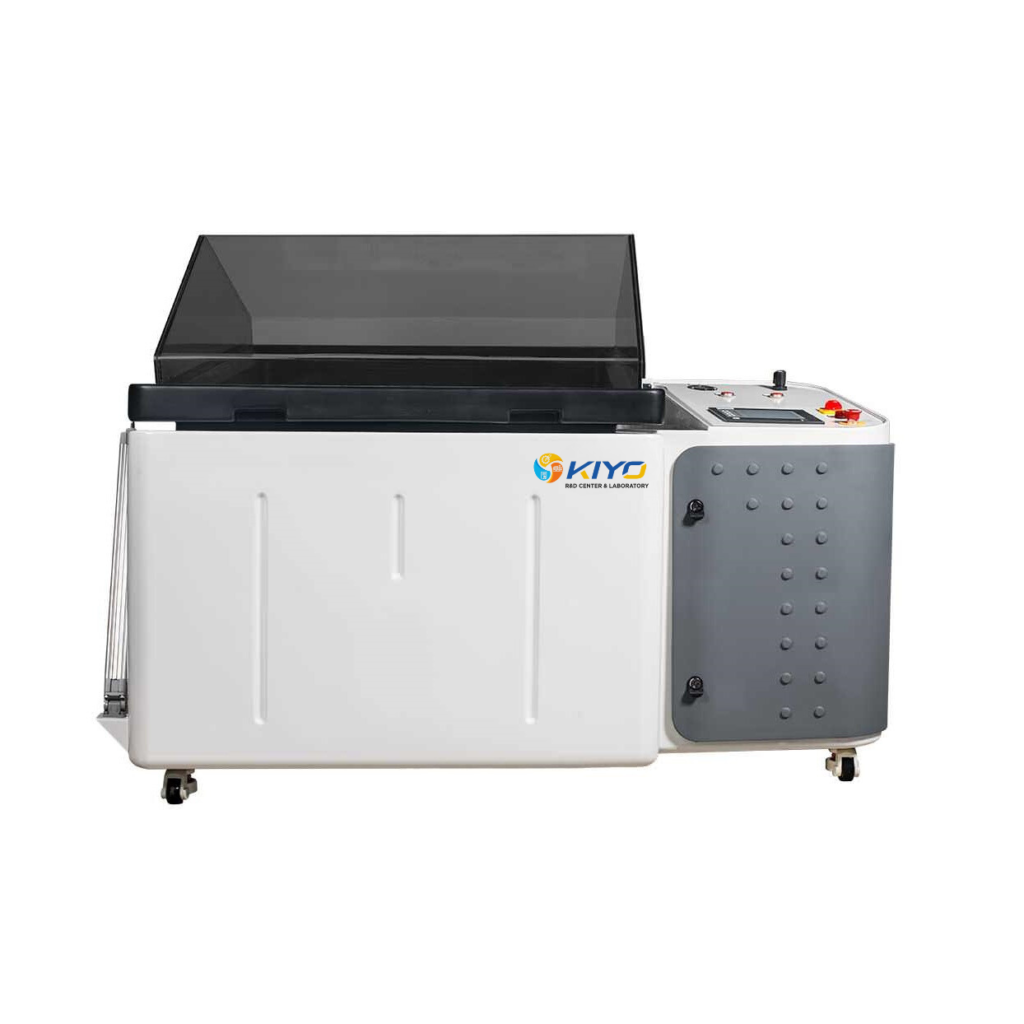
Conclusion
- The Salt Spray Resistance Test, as governed by the MS 655-08 standard, is a critical tool in the arsenal of manufacturers and engineers striving to ensure the durability and reliability of their products. By adhering to this standard, industries can mitigate the risks associated with corrosion, enhance product performance, and ensure compliance with regional and international quality standards.At Kiyo R&D Center & Laboratory, we specialize in conducting Salt Spray Resistance Tests in accordance with MS 655-08, providing you with the insights you need to make informed decisions about your materials and products. Contact us today to learn more about how we can support your testing needs and help you achieve excellence in corrosion resistance.