Heat Cycle Test As Per Standard IEC 61284
Understanding Heat Cycle Testing According to IEC 61284
Introduction
- In the power industry, ensuring the reliability and safety of components used in overhead power lines is crucial. One of the essential tests for validating these components' performance under varying thermal conditions is the Heat Cycle Test as outlined in IEC 61284. This blog will dive into the specifics of what the Heat Cycle Test entails, its significance, and the methodology involved.
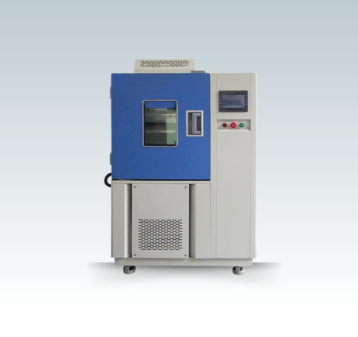
What is IEC 61284?
IEC 61284, developed by the International Electrotechnical Commission (IEC), is a standard that specifies the requirements and testing methods for fittings of overhead electrical lines. This standard encompasses mechanical and electrical properties, including the Heat Cycle Test, which is a pivotal part of assessing how materials react to temperature fluctuations. The goal is to ensure that components can withstand both the typical and extreme thermal stresses they may encounter during their operational lifespan.
Purpose of the Heat Cycle Test
The Heat Cycle Test is designed to simulate the thermal conditions experienced by electrical conductors and fittings over time. These components are exposed to heat due to environmental conditions and electrical load. The key purposes of the Heat Cycle Test are:
- Simulate Real-World Conditions: By mimicking the thermal stresses that components will face, the test helps predict how they will perform under actual working conditions.
- Identify Potential Failures: Detecting material weaknesses and potential points of failure before deployment is crucial for ensuring safety and reliability.
- Enhance Durability: Understanding how materials respond to temperature changes allows manufacturers to improve material formulations and design for enhanced durability.
Heat Cycle Testing Procedure According to IEC 61284
The IEC 61284 standard outlines a structured procedure for conducting Heat Cycle Tests to ensure consistency and reliability in the results. Here’s a step-by-step overview of the typical procedure:
- Preparation of Test Samples: Test samples, which might include conductors, clamps, or other fittings, are prepared according to the specifications provided in IEC 61284. These samples should reflect the actual products to ensure that the test results are representative.
- Defining the Test Parameters: The standard specifies the number of cycles, temperature ranges, and the duration of each cycle. A typical test may involve heating the sample to a specific maximum temperature (often simulating peak operational or fault conditions), holding it there for a set period, and then allowing it to cool to a lower temperature. This cycle is repeated multiple times.
- Execution of Heat Cycles: The samples are placed in a controlled environment where the temperature is systematically cycled between the defined high and low values. The transitions between these temperatures need to be as uniform and controlled as possible to simulate real-world conditions accurately.
- Monitoring and Data Collection: During the test, various parameters are monitored. These may include physical deformation, changes in electrical conductivity, and other relevant mechanical or electrical properties. Accurate data collection is crucial for analyzing the results.
- Post-Test Analysis: After the completion of the heat cycles, the samples are examined for any signs of degradation, such as material fatigue, cracking, or significant changes in electrical or mechanical properties. The results are then analyzed to determine if the components meet the criteria set by IEC 61284.
Key Benefits of Heat Cycle Testing
Heat Cycle Testing under IEC 61284 provides several critical benefits:
- Reliability Verification: By simulating the thermal conditions that components will face, this test helps ensure that only those materials and designs that can withstand such conditions are used in power lines, enhancing overall system reliability.
- Safety Assurance: Preventing in-service failures that could lead to power outages or safety hazards is a primary goal. Heat Cycle Testing identifies weak points that could compromise safety.
- Product Improvement: Test results offer valuable insights for manufacturers to refine materials and designs, resulting in better performance and longer-lasting components.
Challenges and Considerations
While Heat Cycle Testing is crucial, it comes with challenges and considerations:
- Precision in Temperature Control: Achieving precise temperature control during the test is critical. Any deviations can lead to inaccurate test results, affecting the reliability of the conclusions drawn.
- Material Variability: Different materials respond differently to heat cycling. Understanding these variances and ensuring that the chosen materials meet the necessary performance criteria is essential.
- Cost and Time: Heat Cycle Testing can be time-consuming and expensive, especially when conducted on a large scale. Balancing the need for thorough testing with practical considerations of cost and time is necessary.
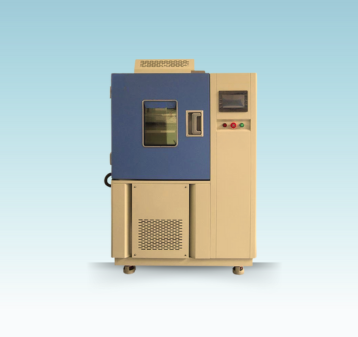
Conclusion
- The Heat Cycle Test as per IEC 61284 is a vital part of the quality assurance process for overhead line fittings. It ensures that the components used can withstand the thermal stresses they will encounter, thereby ensuring the reliability and safety of electrical power distribution networks. As the demand for electricity and the complexity of power grids continue to grow, such rigorous testing standards will remain integral to the development of safe and reliable electrical infrastructure.