Certified Automotive Testing Lab in Chennai
Certified Automotive Testing Lab in Chennai – Where Performance Meets Precision
Introduction
- The automotive industry is driven by innovation, safety, and reliability. Whether you're developing interior trims, engine components, or under-the-hood parts, testing is the foundation of quality assurance. At Kiyo R&D Center & Laboratory, we provide comprehensive testing solutions tailored to the automotive sector — making us a preferred automotive testing lab in Chennai.
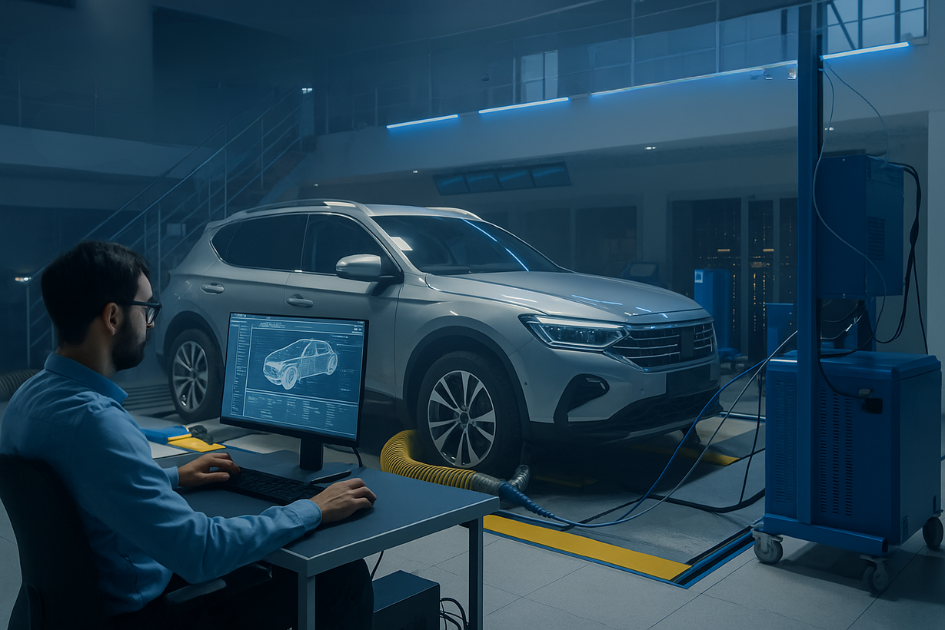
Why Automotive Testing Matters?
Automotive components are exposed to extreme conditions — vibration, heat, friction, and impact. Proper testing ensures that every part performs as expected, even in the toughest environments.
At Kiyo R&D Lab, our testing services help you:
Validate new product designs
Meet safety and compliance standards
Identify performance weaknesses
Support R&D with accurate material analysis
Our Key Automotive Testing Capabilities
We offer a wide spectrum of mechanical, thermal, chemical, and flammability tests for automotive-grade materials and assemblies:
Tensile Testing
Determines the maximum load a material can withstand before breaking. Used for plastic clips, rubber gaskets, and metal fasteners.
Impact Testing (Izod & Charpy)
Assesses a material’s toughness when subjected to sudden force — ideal for bumpers, trims, and molded parts.
FMVSS 302 Flammability Testing
Required for vehicle interiors, this test evaluates how quickly a material burns when exposed to flame. Essential for seat backs, dashboards, and roof liners.
Vibration Testing
Simulates road-induced stress on mechanical or electronic parts. Helps prevent failure in real-world use.
HDT and VSP Thermal Testing
Measures heat resistance and softening point of materials — critical for engine bays, electrical housings, and underbody panels.
Compression & Flexural Testing
Evaluates structural strength, ideal for mounts, bushings, and semi-rigid plastic parts.
Material Characterization (FTIR, TGA, DSC)
Used to understand composition, thermal degradation, and performance behavior of polymers and rubber compounds.
Components We Commonly Test
Door trims and dashboard panels
Electrical cable insulation
Seat covers and headliners
Bumpers, brackets, and mounting parts
HVAC system plastics
Engine covers and under-hood components
Why Choose Kiyo R&D Center & Laboratory?
As a trusted automotive testing lab in Chennai, Kiyo R&D offers a blend of advanced equipment, skilled analysts, and end-to-end testing services.
You Get:
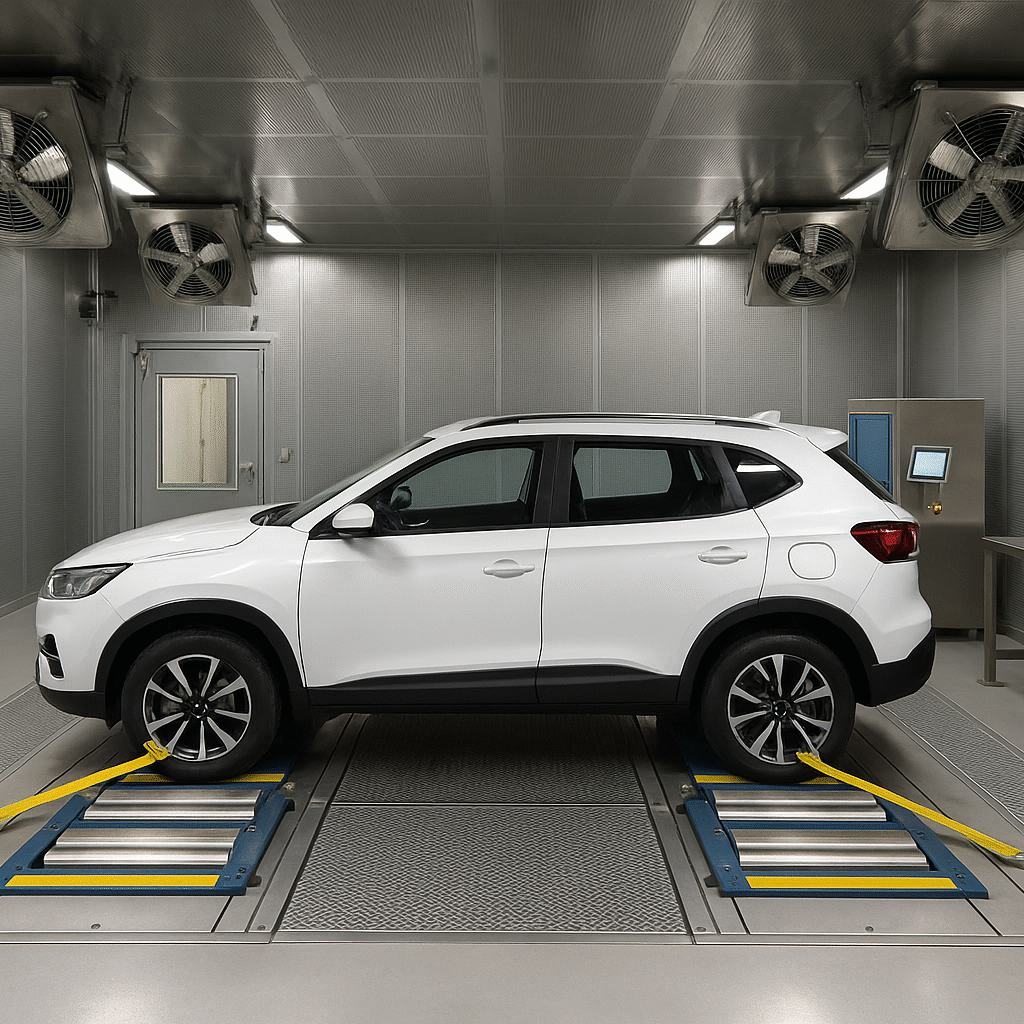
Conclusion
- Every automotive part needs to pass the test — and we make sure it does. From strength to flammability, Kiyo R&D Center & Laboratory delivers precise results to help your components meet the demands of performance, safety, and compliance.