Surface Resistivity Test in Chennai
Empowering Chennai’s Industries with Surface Resistivity Testing
Introduction
- As electronic devices and advanced polymers become integral to modern manufacturing, ensuring their electrical performance is no longer optional—it’s essential. Surface resistivity testing has emerged as a critical quality control step for industries aiming to safeguard their products against electrostatic damage, contamination, and electrical failures. In Chennai, a city synonymous with industrial growth, the demand for this specialized testing is gaining momentum.
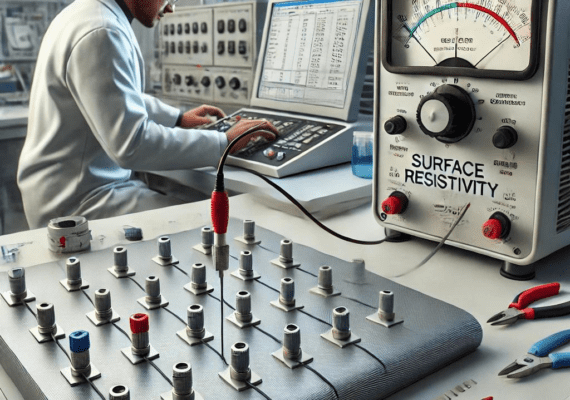
What is Surface Resistivity?
Surface resistivity refers to how much a material resists the flow of electrical current across its surface. For materials used in circuit boards, electronic housings, automotive components, and packaging, maintaining appropriate resistivity levels ensures both performance and safety. This is especially relevant in electronics manufacturing and ESD (Electrostatic Discharge) control applications.
Why Industries in Chennai Rely on This Test
Chennai is home to a diverse industrial base—from IT and electronics to automotive and aerospace. For these sectors:
Static protection is a top priority in sensitive manufacturing environments.
Material qualification must comply with international electrical insulation standards.
Innovation and reliability depend on accurate material behavior predictions.
Surface resistivity testing enables companies to:
Evaluate material consistency
Prevent ESD-related failures
Validate compliance with global regulations like ASTM D257
Leading the Way: Local Testing Excellence
Chennai’s laboratories, like Kiyo R&D Center & Laboratory, are equipped with the latest resistivity testing systems, ensuring accurate measurement even for high-impedance materials. These labs often support:
Polymeric compound developers
Packaging material manufacturers
Automotive and electronics OEMs
With precise instrumentation and strict procedural standards, clients receive reliable data crucial for product design, process control, and certification.
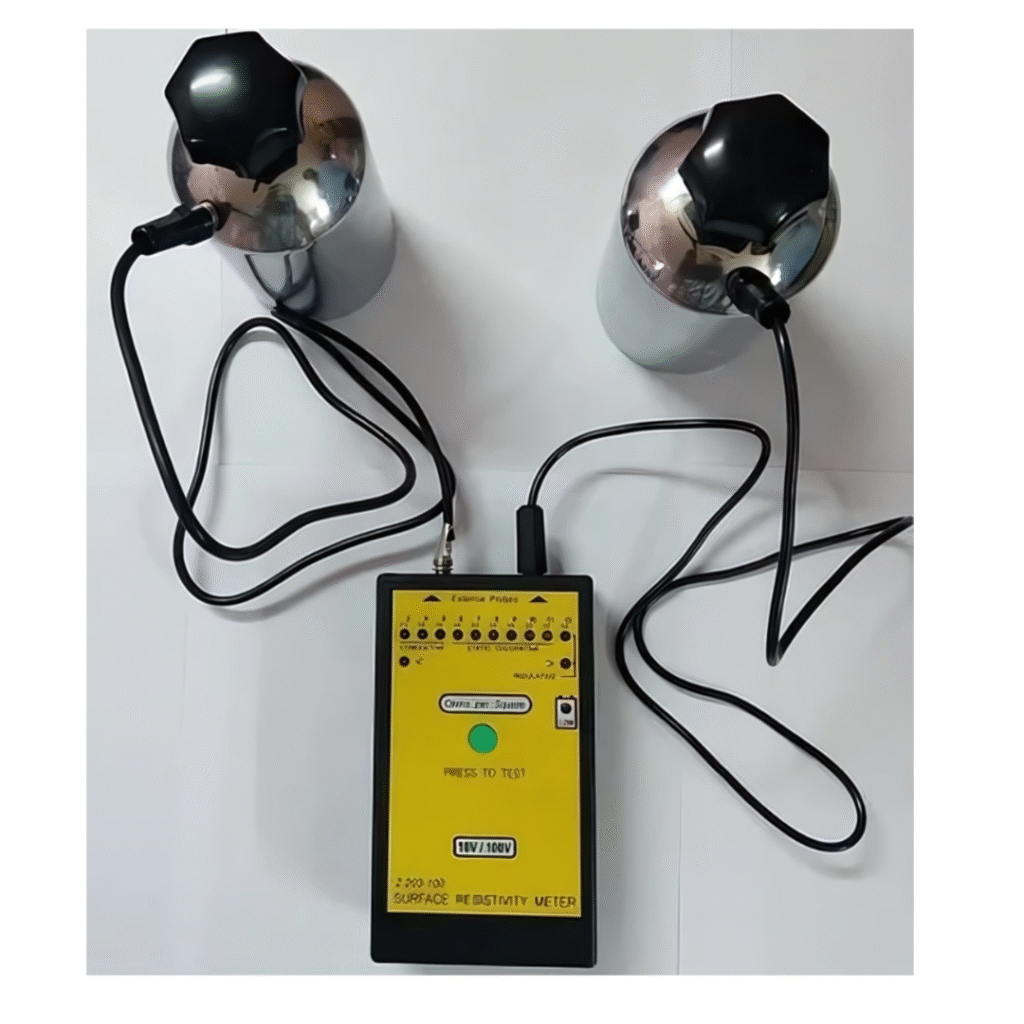
Conclusion
- As Chennai's manufacturing landscape continues to modernize, surface resistivity testing will become increasingly integrated into routine material assessments. Companies prioritizing this analysis gain a competitive edge—offering safer, more durable, and regulation-compliant products.