Brittleness Temperature Test As Per Standard ASTM D746
Understanding Brittleness Temperature Testing with ASTM D746
Introduction
- When designing products that must perform reliably in cold environments, selecting materials that can withstand low temperatures without becoming brittle is crucial. The Brittleness Temperature Test, defined by ASTM D746, is a standard test method that helps determine the temperature at which materials, especially plastics and elastomers, become brittle and are likely to fracture. This test is essential for ensuring product durability and safety in industries ranging from automotive to consumer goods.
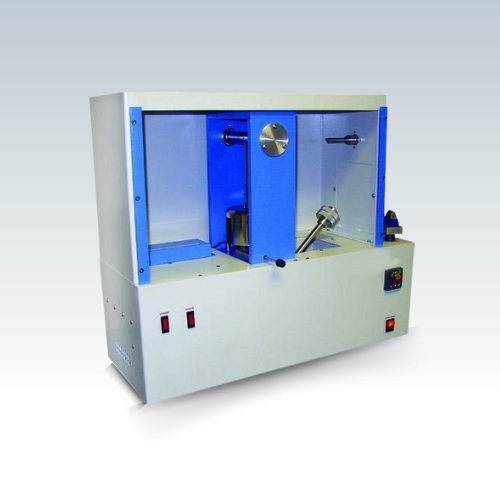
What is ASTM D746?
ASTM D746, formally titled Standard Test Method for Brittleness Temperature of Plastics and Elastomers by Impact, is an internationally recognized standard. It establishes a procedure for determining the temperature at which a material, when subjected to an impact, shows brittle failure. The test identifies the brittleness temperature, which is defined as the highest temperature at which 50% of the specimens tested exhibit brittle failure under specified conditions.
Why is Brittleness Temperature Important?
Brittleness temperature is a critical parameter for materials that need to perform in sub-zero environments. Knowing this temperature helps manufacturers choose the right materials for applications where exposure to low temperatures could compromise the material’s integrity and performance. If a material becomes brittle and fractures under impact at a specific low temperature, it could lead to product failure, potentially causing safety hazards, costly recalls, or damage to a brand’s reputation.
The Testing Procedure
The brittleness temperature test involves the following steps:
- Specimen Preparation: Specimens are prepared according to the standard dimensions specified by ASTM D746. The consistency in specimen size ensures the reliability and comparability of test results.
- Cooling: The test specimens are cooled to a series of predetermined temperatures using a controlled cooling system. A common cooling medium is a mixture of dry ice and alcohol, which allows for precise temperature control.
- Impact Test: Once cooled to the target temperature, each specimen is subjected to an impact load using a standardized testing apparatus. The impact simulates real-world conditions that the material might experience.
- Observing Failure: The specimens are examined for signs of brittle failure—typically cracking or shattering. The brittleness temperature is determined as the temperature at which 50% of the specimens fail under the impact.
Key Factors Influencing Brittleness Temperature
Several factors can affect the brittleness temperature of materials:
Material Type and Composition: Different polymers and additives can influence how a material reacts to low temperatures. For example, adding rubber to a plastic can lower its brittleness temperature, making it more suitable for cold environments.
Specimen Thickness: The thickness of the test specimen can affect how quickly it reaches the test temperature and how it distributes stress under impact. Thicker specimens might show different brittleness temperatures compared to thinner ones.
Cooling Rate: The speed at which the specimens are cooled can influence test outcomes. Rapid cooling might result in higher brittleness temperatures compared to slower cooling rates, as it might not allow the material to reach thermal equilibrium.
Environmental Exposure and Aging: Materials that have been exposed to sunlight, moisture, or chemicals over time might exhibit changes in their brittleness temperature, either becoming more brittle or less, depending on the environmental factors.
Applications of ASTM D746 Brittleness Testing
Automotive Parts: Components such as bumpers, hoses, and seals are often exposed to cold weather. Testing ensures these parts remain flexible and do not crack, maintaining vehicle safety and performance.
Building and Construction: Materials like exterior panels, pipes, and insulation must withstand cold climates without failing. The brittleness temperature test helps identify materials that will perform well in these conditions.
Consumer Products: Products such as sports equipment, storage containers, and outdoor gear are used in various environments. Ensuring these items don’t fail in cold conditions is critical for user safety and product reliability.
Electronics: Components in electronic devices, especially those used outdoors or in cold storage, need to maintain integrity under low-temperature conditions. Brittleness temperature testing helps in selecting suitable materials.

Conclusion
- ASTM D746 Brittleness Temperature Testing is a crucial method for determining the suitability of materials for low-temperature applications. By understanding how and when materials become brittle, manufacturers can make informed decisions, ensuring their products are safe, reliable, and fit for purpose even in the coldest environments. As industries advance and push the limits of material applications, tests like these ensure that safety and performance remain uncompromised.