Exploring the Tensile Strength of Rubber: A Comprehensive Guide
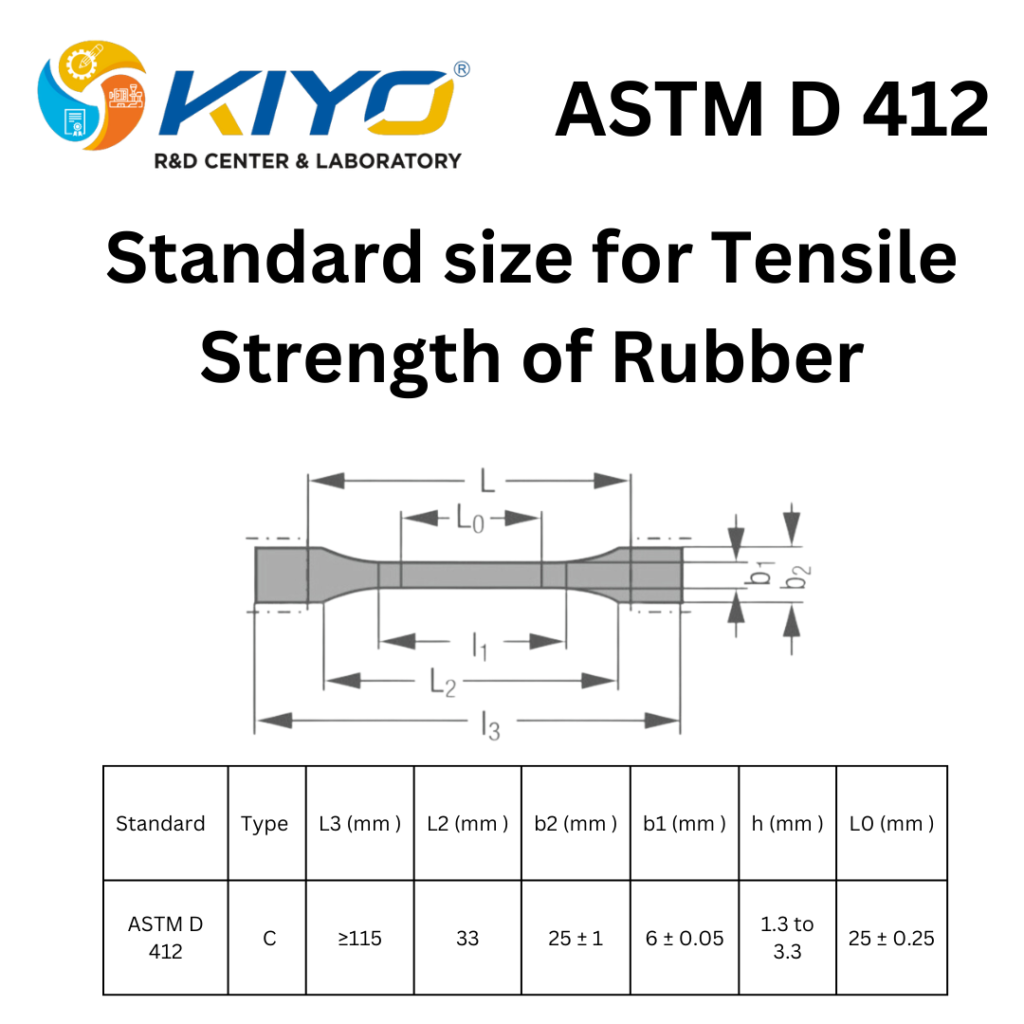
Introduction to Rubber’s Versatility
Rubber and elastomeric materials are celebrated for their remarkable versatility and durability, finding applications in industries ranging from automotive to healthcare. What gives rubber its unique set of properties, and how can these be quantified to ensure the material meets the specific needs of these diverse applications? The answer lies in understanding the tensile strength of rubber—a critical measure of its performance.
The Role of ASTM D 412 in Measuring Tensile Strength
ASTM D 412 is the gold standard for determining the tensile properties of vulcanized rubber and thermoplastic elastomers. This method meticulously evaluates tensile strength, elongation, and stress-strain behavior, offering a window into the material’s capabilities. However, it’s crucial to note that ASTM D 412 does not prescribe specific tensile strength values. Instead, it provides a framework for testing, leaving the actual values to be defined by the material’s composition and the test conditions.
The Significance of Tensile Strength
Tensile strength represents the maximum amount of tensile stress that a material can withstand before failure. For rubber, this metric is pivotal, dictating how well the material can maintain its integrity under stretch and stress. Whether it’s a tire enduring the rigors of the road or a medical device flexing within the human body, tensile strength ensures that rubber can perform reliably under pressure.
Navigating the Range of Tensile Strengths
Given the diversity of rubber compounds, tensile strength can vary significantly. Here’s a snapshot of average tensile strengths for some common types of rubber, showcasing the broad spectrum of performance:
- Natural Rubber (NR): 20 to 30 MPa
- Styrene-Butadiene Rubber (SBR): 2 to 30 MPa
- Nitrile Rubber (NBR): 10 to 30 MPa
- Ethylene Propylene Diene Monomer (EPDM): 8 to 20 MPa
- Silicone Rubber: 5 to 12 MPa
These figures highlight the adaptability of rubber materials, engineered to meet the demands of specific applications through meticulous formulation and testing.
Conclusion: The Importance of Precision and Testing
The journey to selecting the right rubber material for any application begins and ends with precise testing and a deep understanding of tensile strength. ASTM D 412 serves as a crucial guide in this process, ensuring that materials are rigorously evaluated and chosen based on their ability to meet the demands of their intended use. By delving into the specifics of tensile strength, engineers and designers can unlock the full potential of rubber, creating products that not only perform exceptionally but also push the boundaries of what’s possible.