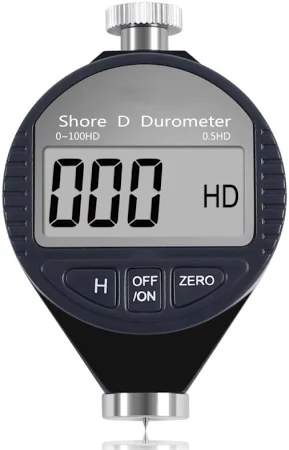
In the vast world of material science and quality assurance, hardness testing stands as a cornerstone for evaluating the mechanical properties of various materials. Among the myriad of methods available, Shore A and Shore D hardness testing emerge as fundamental techniques, particularly within the rubber and plastics industries. This essay endeavors to provide a comprehensive analysis of Shore A and Shore D hardness testing, encompassing their principles, standards, significance, specimen size, and applications.
Hardness testing, named after its inventor Albert F. Shore, is a method used to measure a material’s resistance to indentation. This measurement offers valuable insights into properties such as flexibility, resilience, and wear resistance, making it an essential aspect of quality control processes. Shore hardness testing is renowned for its simplicity, speed, and non-destructive nature, making it highly favored across industries.
Shore A hardness testing is primarily employed for elastomers and rubbers, utilizing a spring-loaded indenter with specific geometry. Standardized procedures for Shore A hardness testing are detailed in ASTM D2240 and ISO 868 standards. The specimen size recommended for Shore A hardness testing is typically a minimum of 6.35 mm (0.25 inches) in thickness and large enough to accommodate the indenter. Results are expressed as Shore A durometer values ranging from 0 to 100, with higher values indicating greater hardness.
Conversely, Shore D hardness testing is tailored for harder materials such as plastics and rigid elastomers, employing a denser, sharper indenter. Similar to Shore A, ASTM D2240 and ISO 868 provide standards for Shore D hardness testing. The specimen size recommended for Shore D hardness testing is also typically a minimum of 6.35 mm (0.25 inches) in thickness and large enough to accommodate the indenter. Results are presented as Shore D durometer values ranging from 0 to 100.
The significance of Shore hardness testing transcends various industries, with applications ranging from quality control and material selection to product development and comparative analysis. In quality control processes, Shore hardness testing ensures the consistency of material properties and compliance with industry standards, fostering confidence in product performance and reliability. Moreover, it facilitates the selection of appropriate materials based on desired hardness characteristics, guiding engineers and designers in optimizing product formulations and enhancing overall performance. In research and development endeavors, Shore hardness testing serves as a valuable tool for fine-tuning material compositions, exploring new applications, and driving innovation. Additionally, comparative analysis facilitated by Shore hardness testing enables industries to make informed decisions regarding material substitution, process optimization, and performance enhancement.
In conclusion, Shore A and Shore D hardness testing are indispensable techniques in material science and quality assurance. Their ability to provide quantitative measures of material hardness, as standardized by ASTM D2240, ISO 868, and other relevant standards, makes them invaluable across various industries. By understanding the principles, standards, significance, specimen size, and applications of Shore hardness testing, industries can ensure standardized testing procedures, reliable results, and continued innovation in material development and product manufacturing.