Wear Resistance Testing As Per Standard ASTM D4213
Enhancing Material Durability Through ASTM D4213 Wear Resistance Testing
Introduction
- In today's competitive market, ensuring the durability of products is crucial for maintaining customer satisfaction and reducing maintenance costs. Wear resistance testing is an essential process for understanding how materials will hold up under everyday use. ASTM D4213 is a widely recognized standard for testing the wear resistance of coatings, particularly those used in architectural and industrial applications. This blog will explore the significance of ASTM D4213, the methodology it involves, and its application across different industries to enhance product durability.
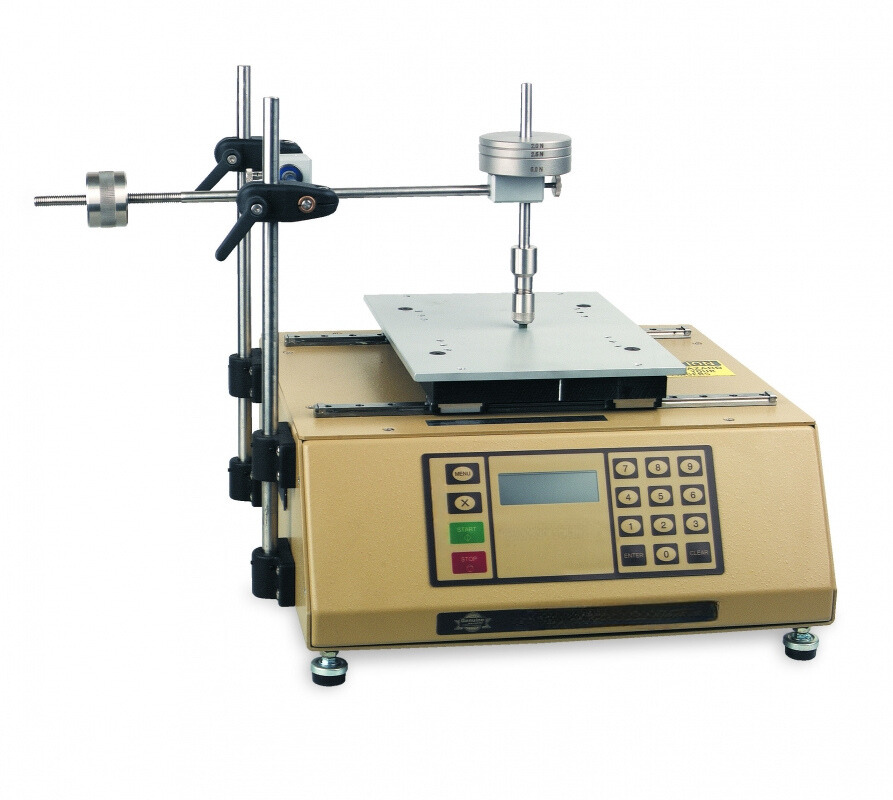
What is Wear Resistance Testing?
Wear resistance testing measures a material’s ability to withstand abrasion and mechanical wear. This property is vital for materials and coatings subjected to frictional forces, such as wall paints, protective coatings, automotive finishes, and fabrics. By replicating the conditions under which materials are expected to perform, wear resistance testing helps manufacturers predict product lifespan and identify areas for improvement.
ASTM D4213: The Standard for Wear Resistance Testing
ASTM D4213, also known as the Standard Test Method for Scrub Resistance of Wall Paints, provides a procedure for evaluating the wear resistance of a material’s surface using a scrub resistance tester. This standard is particularly valuable for testing paints and coatings, allowing manufacturers to assess how well these finishes can withstand repeated cleaning and abrasion.
Key Aspects of the ASTM D4213 Test Method
- Sample Preparation: A sample coating is applied to a standardized panel and allowed to dry or cure. This step ensures the coating is tested in a state that closely mirrors real-world applications.
- Testing Apparatus: The scrub resistance tester, a key piece of equipment, features a brush or abrasive pad that simulates the wear process. This apparatus is designed to provide consistent and controlled wear conditions across different samples.
- Abrasive Medium and Conditions: The test involves an abrasive brush or pad, often combined with a specific cleaning agent, that moves back and forth across the coated panel. The number of cycles and the pressure applied are standardized to ensure repeatable results.
- Evaluation: After completing a set number of cycles, the test panel is examined for signs of wear, such as the loss of gloss, coating degradation, or substrate exposure. Measurements of coating thickness before and after the test can provide quantitative data on the wear resistance.
Importance of ASTM D4213 Wear Resistance Testing
Product Quality Assurance: ASTM D4213 helps manufacturers ensure their coatings and finishes meet specific quality standards. By understanding wear resistance, manufacturers can offer products that stand up to the rigors of daily use.
Extended Product Life: Products that pass wear resistance tests are likely to have a longer service life, which can lead to reduced maintenance and replacement costs for end-users.
Consumer Confidence: For consumers, knowing a product has undergone rigorous wear resistance testing can increase confidence in its durability and value, leading to higher satisfaction and brand loyalty.
Regulatory Compliance: Many industries have specific standards and regulations regarding material durability. ASTM D4213 provides a recognized benchmark for meeting these requirements, ensuring compliance and avoiding potential legal issues.
Applications of ASTM D4213
- Architectural Finishes: In the building industry, wall paints and coatings must endure frequent cleaning without degrading. ASTM D4213 testing helps manufacturers develop products that can withstand repeated scrubbing without losing their aesthetic appeal or protective qualities.
- Automotive Industry: Coatings used in vehicles are exposed to harsh environmental conditions and physical wear. Wear resistance testing ensures these coatings maintain their appearance and function over time, even under demanding conditions.
- Textiles and Upholstery: Fabrics used in furniture and automotive interiors can benefit from wear resistance testing to ensure they remain looking new and intact despite regular use and cleaning.
- Industrial Equipment: Protective coatings on machinery and tools must resist wear to prevent corrosion and maintain functionality. ASTM D4213 testing helps in selecting and developing coatings that enhance equipment durability.
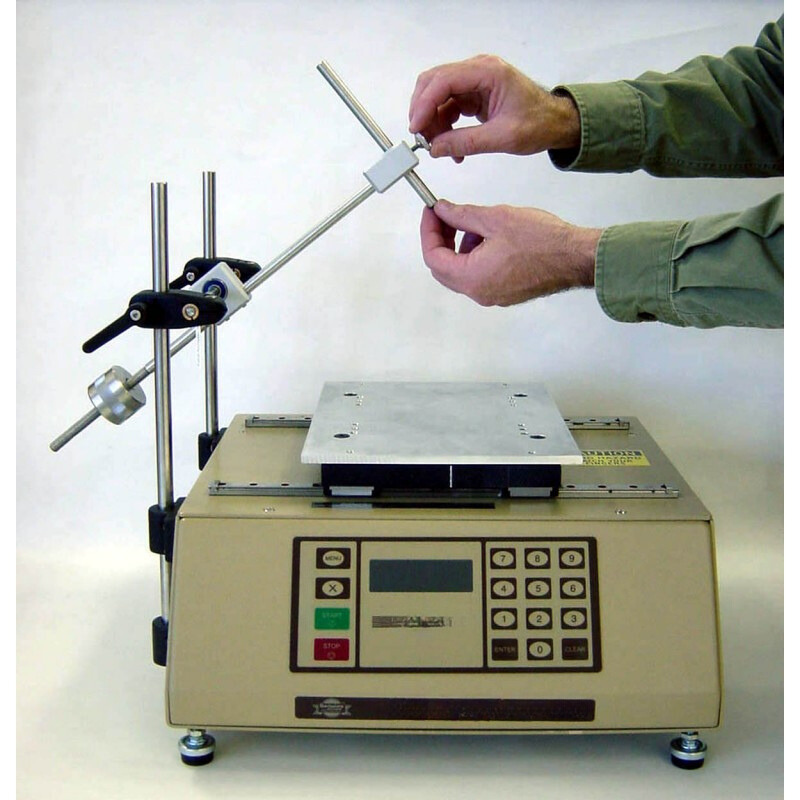
Conclusion
- Wear resistance testing using the ASTM D4213 standard is an integral part of product development and quality assurance across various industries. By simulating real-world wear conditions, this test method provides valuable insights into a material's durability and helps manufacturers create long-lasting products. Whether it's architectural coatings, automotive finishes, or industrial equipment, understanding wear resistance through ASTM D4213 testing is key to enhancing product performance and longevity.