Adhesion Test As Per Standard MS 655-08
Comprehensive Guide to Adhesion Testing per MS 655-08
Introduction
- Adhesion testing is a vital process used to determine the strength of the bond between a coating and its substrate. This is particularly crucial in industries such as automotive, aerospace, and construction, where the integrity of coatings directly impacts the performance and durability of products. The MS 655-08 standard outlines a rigorous procedure for adhesion testing, ensuring consistent and reliable results. In this blog, we will explore the detailed methodology of adhesion testing as per MS 655-08, the equipment used, and the interpretation of test results.
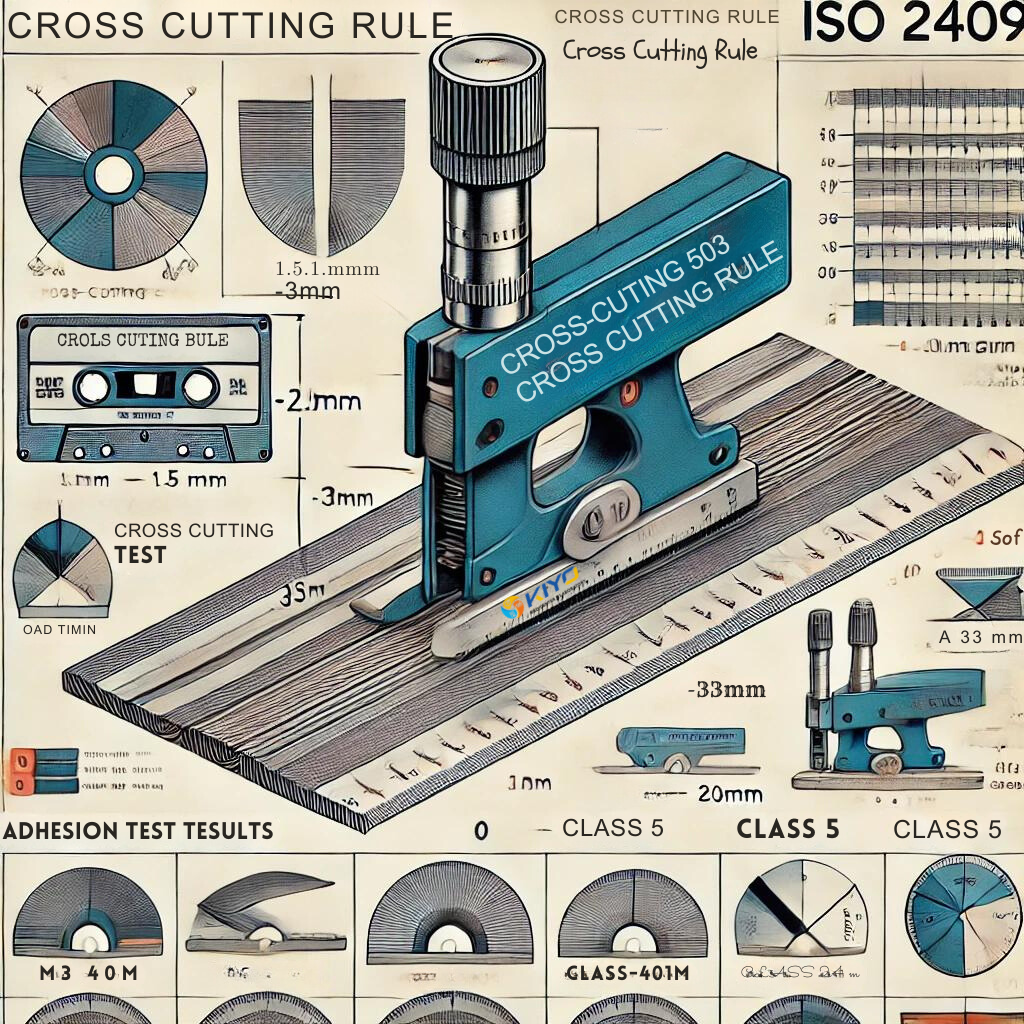
Importance of Adhesion Testing
Adhesion testing helps to evaluate the performance of a coating under various conditions. Poor adhesion can lead to coating failure, resulting in exposure of the substrate to environmental elements, which can cause corrosion and other forms of degradation. By following the MS 655-08 standard, industries can ensure that their coatings adhere properly and provide long-term protection.
Equipment Required
The primary tool used in adhesion testing as per MS 655-08 is the BGD 503 Cross Cutting Rule. This instrument is designed for precision and accuracy, ensuring that the cuts made on the coating are consistent and meet the specified standards. Here are the main technical parameters of the BGD 503:
- Cutting Distance: Options of 1mm, 1.5mm, 2mm, 3mm
- Cutting Length: 35mm
- Number of Cutting Teeth: 11
- Single-Blade Cutter: V-shaped cutting edge (15° ~ 30°)
- Blade Thickness: 0.43 ± 0.03mm
Step-by-Step Procedure
- Specimen Preparation:
- Ensure the specimen is placed on a stable, horizontal surface.
- Position the cutter guide on the specimen surface.
- Making the Cuts:
- Use the cutter knife to create a cross-cut pattern (10×10) on the coating. Each cut should have a spacing of 2mm. The cutter knife must be held at an angle of approximately 30 degrees to ensure the cuts penetrate the coating and reach the substrate.
- Applying Adhesive Tape:
- Within 5 minutes of making the cuts, apply cellophane tape to the cross-cut area. The tape should conform to JIS Z 1522 standards and be 24mm wide.
- Peeling the Tape:
- Quickly pull the tape at a 90-degree angle within 0.5 seconds after application. This action will remove any loose coating from the substrate.
- Evaluating the Results:
- Inspect the cross-cut area for signs of flaking or delamination. The extent of the coating removal is then classified according to the MS 655-08 standard.
Classification of Results
The MS 655-08 standard provides a detailed classification system to interpret the results of the adhesion test. This classification ranges from M-1.0 to M-6.0, correlating with the ISO 2409 standards (CLASS 0 to CLASS 5). Here’s a breakdown of the classifications:
M-1.0 (ISO 2409 CLASS 0):
- No flaking at the edges of cuts.
- No exfoliation at intersections.
- Less than 50% delamination per cross-cut area.
M-2.0 (ISO 2409 CLASS 1):
- Small flakes at the edges of cuts.
- No exfoliation at intersections.
- Less than 50% delamination.
- Maximum 5% exfoliation at edges.
M-3.0 (ISO 2409 CLASS 2):
- Flakes at the edges of cuts.
- Exfoliation at intersections.
- Less than 50% delamination.
- Total delamination greater than 5%, but not exceeding 15%.
M-4.0 (ISO 2409 CLASS 3):
- Considerable exfoliation at intersections.
- Delamination area about 5%.
- Total delamination greater than 15%, but not exceeding 35%.
M-5.0 (ISO 2409 CLASS 4):
- Significant exfoliation at edges.
- Delamination area about 20%.
- Total delamination greater than 35%, but not exceeding 65%.
M-6.0 (ISO 2409 CLASS 5):
- Complete delamination over the cross-cut area.
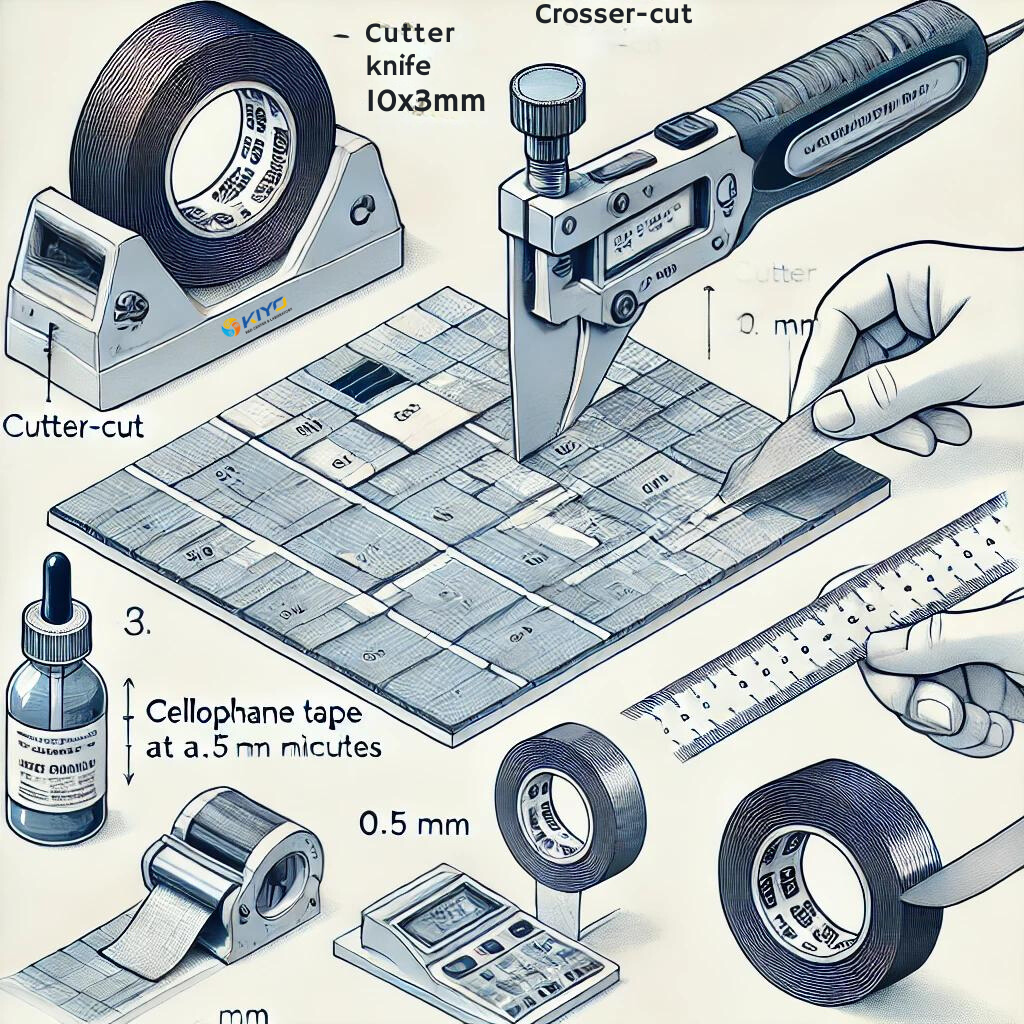
Conclusion
- Adhesion testing as per MS 655-08 is a critical procedure for ensuring the durability and performance of coatings. By following this standardized method, industries can reliably assess the quality of their coatings and make necessary improvements. This not only enhances product longevity but also ensures safety and customer satisfaction. Whether in automotive, aerospace, or construction, adherence to the MS 655-08 standard helps maintain the highest quality standards for coated materials.